Unique tooling design enables near-net shape along with high dimensional accuracy and surface smoothness. Our cold forming techniques achieve tight tolerances, higher fatigue strength, lower weight and intricate shapes. Compared with warm or hot forming, cold forming is characterized by a high degree of processing accuracy with a reduction in manufacturing steps. Tooling dies last longer, there is less scrap and material is not being wasted. This offers big gains in production efficiency and cost reduction.
PROCESS BENEFITS
- High Degree of Processing Accuracy
- Reduction of Manufacturing Steps
- Lower Cost through Greater Production Efficiency
- Tight Tolerances
- Intricate Shapes
FORMING CAPABILITIES
- Tubular Parts: 8-30mm x L 50-1,000mm
- Electrical Parts: 3-12mm x L 5-300mm
- Through Bolts: 3-12mm x 1,000mm
- Custom By Shape
MATERIALS | BEARING STEEL | CARBON STEEL | STAINLESS STEEL | BRASS | ALUMINUM |
FINISHES | TRIVALENT CHROMATE | ZINC | NICKEL | NICKEL CHROME | COPPER | PHOSPHATE | GEOMET* | LOCKPATCH |
Features & Benefits
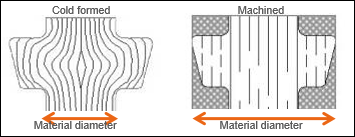
Maintains continuous fiber flow for increased part strength. Eliminates rough surface and potential chipping or fatigue cracks found in machined parts.
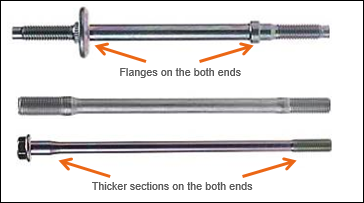
Open die enables flanges and/or thicker sections on both ends. The thicker section is higher strength and thinner center focuses on ductility. Suitable for applications with high tension and vibration.